Keller UK called on the expertise of colleagues from abroad to come up with an innovative solution to create an underground testing pit at and oil and gas facility.
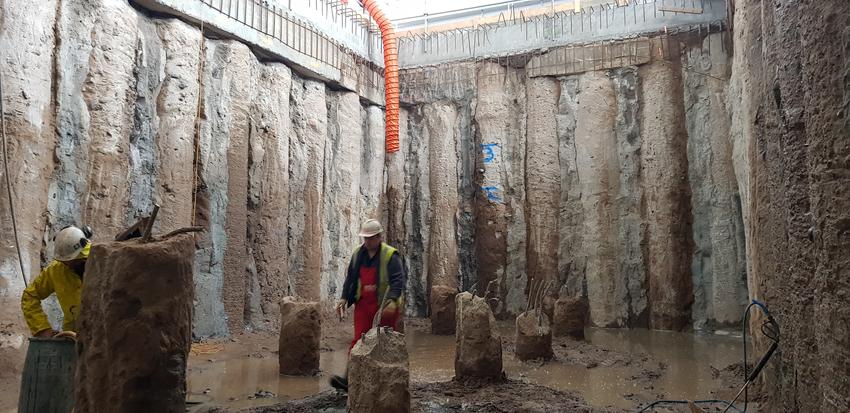
The project
MTM Construction carried out works at Baker Hughes (part of General Electric) to create a Centre of Excellence at their Montrose Campus to support the oil and gas industry. During the construction within the live compound, there was a need to construct foundations to support a new shed facility and its underground testing pit.
The challenge
The need for a complex foundation solution was outlined by design build contractor Canale Associates and consultants Ramsay and Chalmers, who involved Keller for advice from an early stage. The secant box methodology was a new technique to Keller UK but one which has been successfully utilised in other business units across the world. Due to the challenging ground conditions of dense, saturated sandy strata, a hybrid solution was devised.
The solution
The 900mm diameter CFA piles were installed first with the jet grout columns being sized to seal between the piles and construct the watertight wall. A further 88No plug columns were then installed, up to a diameter of 2.2m to create the base of the box. There were two levels of grouting, the 2m deep plug 12m below ground level to resist hydrostatic uplift and another at 7.5m below ground level to act as a dry working platform for MTM to construct the permanent slab. Static load testing was undertaken on 1% of the installed bearing piles along with 100% integrity testing. This combined with a strict QA regime during the jet grout operations provided the client with a fit-for-purpose solution upon completion.
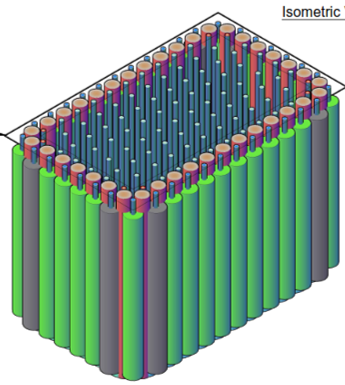
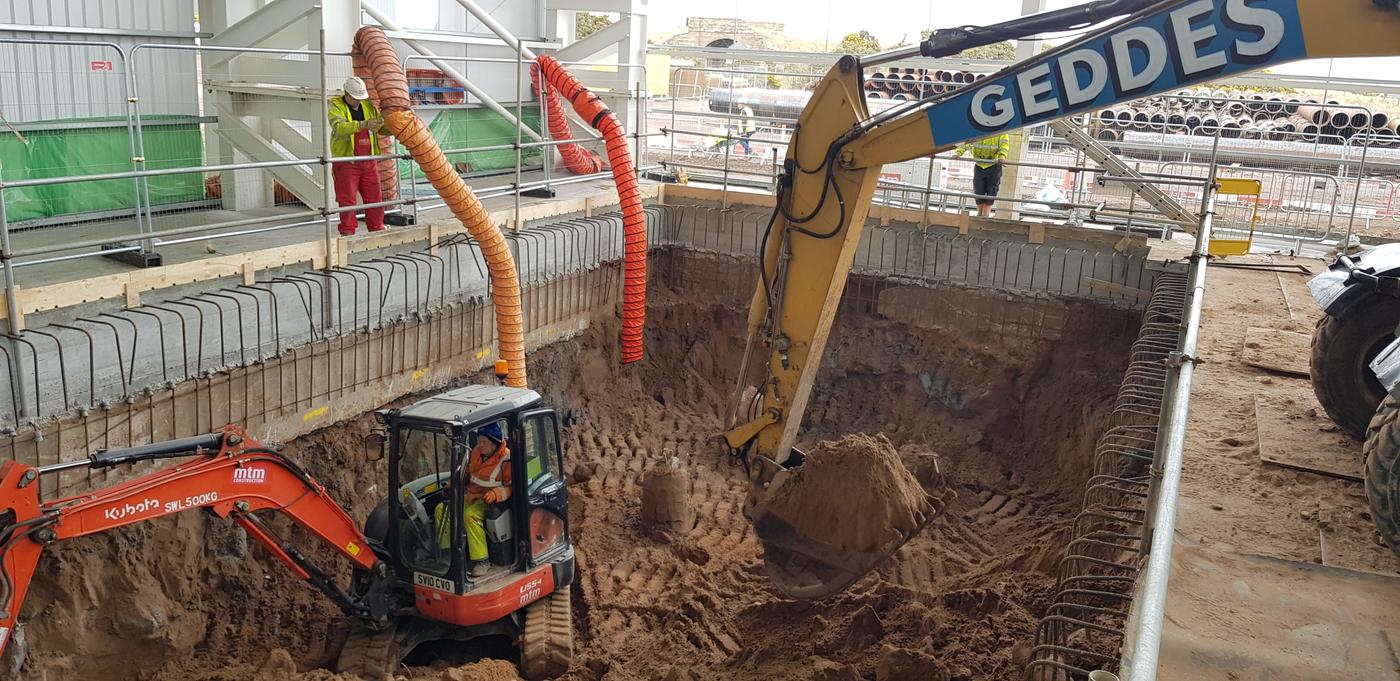
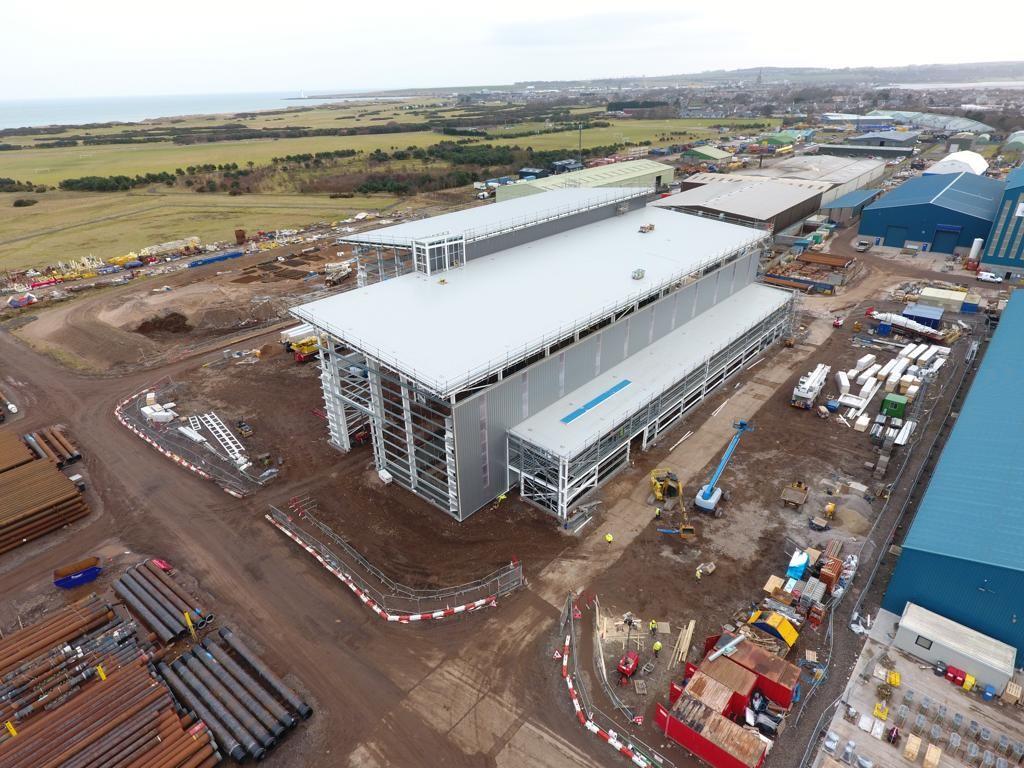